Engineering
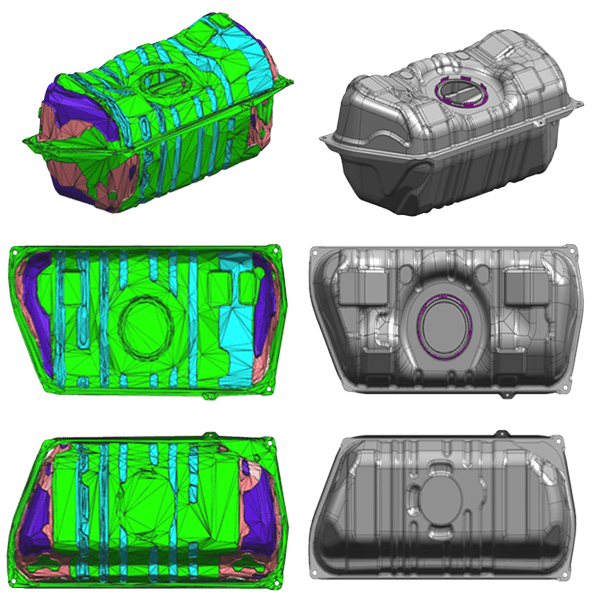
- Computer Aided Engineering (CAE)
- Spectra Premium’s expertise in the application of advanced computer aided engineering (CAE) methods enables mass, volume, and performance optimization to levels only recently attainable. Our team conducts component and system-level laboratory testing based on rigorous standards established by our automotive customers.
- Forming simulation
- This tool precisely models the forming process used for tank shells to ensure a repeatable, stable process that strictly controls part quality. Thickening, necking, and other properties are also measured.
- Topology
- An advanced, free-form structural analysis tool defines the optimal location of structural supports and load carrying features. The results are then interpreted by the product engineering & manufacturing teams to define a production feasible design.
- Topography
- A structural analysis tool which defines optimal rib and bead patterns to maximize the load carrying capability of the tank shell. This tool is used in conjunction with Gauge Optimization to determine the thinnest feasible tank thickness.
- Durability Analysis
- Durability analysis is conducted to determine fatigue life. This cyclical life is determined for both pressure-vacuum and shake/vibration fatigue specifications.
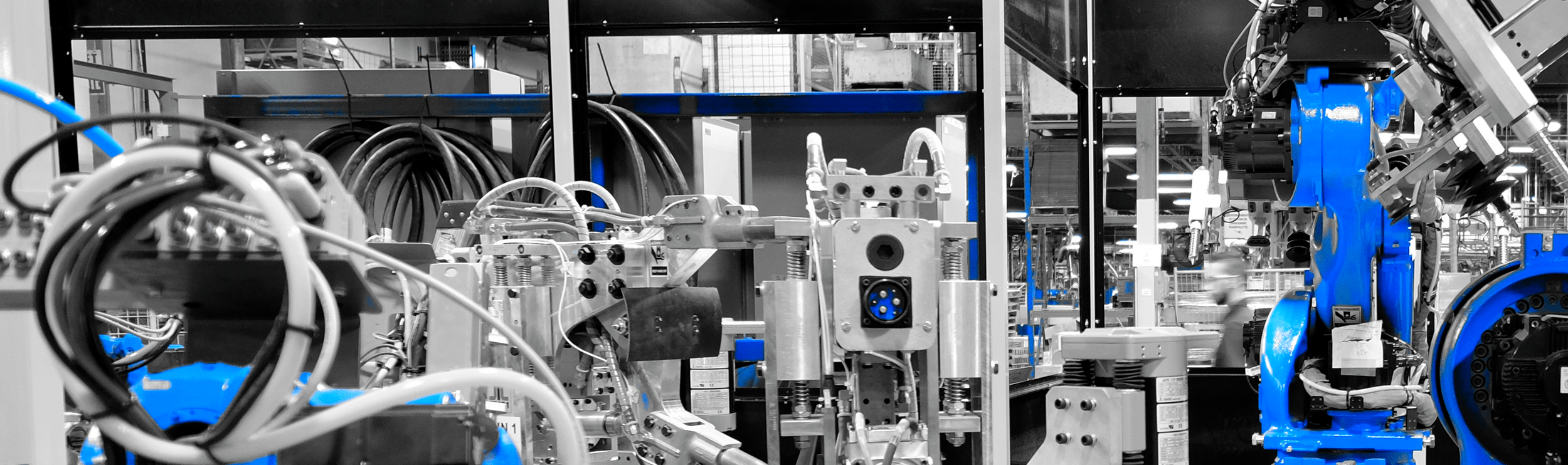
Product Design
Our full in-house capability in both Catia V5 and NX drives our product design, which supported by our dedicated customer CAD/PLM connectivity to carry out data management and release responsibilities. With their sheet metal forming simulation expertise, our in-house team of designers and engineers are committed to all the following aspects of fuel tank product development:
- Shell, baffle, and strap design
- Component packaging
- Grade venting studies
- Mass optimization through topography and topology
- Forming simulations
- Cyclic fatigue simulations
- DFM/DFA
- Prototyping
- Planning and management of DV and PV testing.
Product Development
The development team leads the fuel tank system engineering, design, and validation processes. The team has experience in the development of a wide variety of fuel systems for many vehicle applications including gasoline, diesel, hybrid and plug-in hybrid (PHEV).
- Structured product development process uses a stage gate approach supported by Siemens Teamcenter (PLM)
- Design team fully supports Catia V5 and Siemens NX (Unigraphics) platforms, including dedicated connectivity to Ford Teamcenter, GM Teamcenter, and Chrysler systems
- In-house team dedicated to fuel tank system engineering
- Leads all engineering activity, including design and prototyping
- Fatigue life of steel components is accurately predicted using computational methods
- Experienced in the use of FEA to support the design and development process